Optimize Your Operational Cost
Many organizations striving to reduce operational costs begin by proposing high-cost, high-investment ideas. However, such ideas are often denied or delayed due to the limitation of financial and other resources, which need to be allocated to revenue-generating areas keeping the operational costs high. Operational costs are the result of interaction between people, processes and systems in place. Organizations need to adopt a gradual approach that takes into account people, processes, and systems and how they interact when looking to reduce operational costs.
The initial step should be to ensure that personnel with a target-oriented focus, expertise, capacity for guidance, and most importantly, a high standard of integrity, are placed in all areas. Appointing the appropriate people to manage operations and related costs can be a primary source of savings. Often, a slight reorganization can accomplish the desired outcome. By focusing on people first, organizations can ensure that the right resources are in place to manage costs and follow processes in place.
The second important area to evaluate is the processes. Evaluating processes is a critical aspect of any operation. Poorly defined processes, or processes that are not properly adhered to, can result in costly mistakes, pilferage and expensive decisions, all of which can be attributed to a lack of visibility, responsibility and accountability in the supply chain management process. Vendor management processes and contract management being inadequate contributes to elevated costs and complications. To identify areas where improvements can be made, it is essential to review existing processes and ensure that the right people are in place to carry out the necessary tasks.
Upon proper implementation of the necessary personnel and processes, the deployment of a system to assist people in following the established processes and realizing further cost savings can yield significant results. In many cases, the requisite system is already available, but is not being used efficiently or needs to be adapted to satisfy new requirements. An extensive review of existing resources and personnel could potentially reveal that major components are already available or can be created internally, without having to purchase costly external solutions.
Investigating the potential of existing resources before making a major decision to invest in new technology or systems can bring immediate results, as well as garner the approval of senior management for further investments which are likely to yield greater operational efficiency.


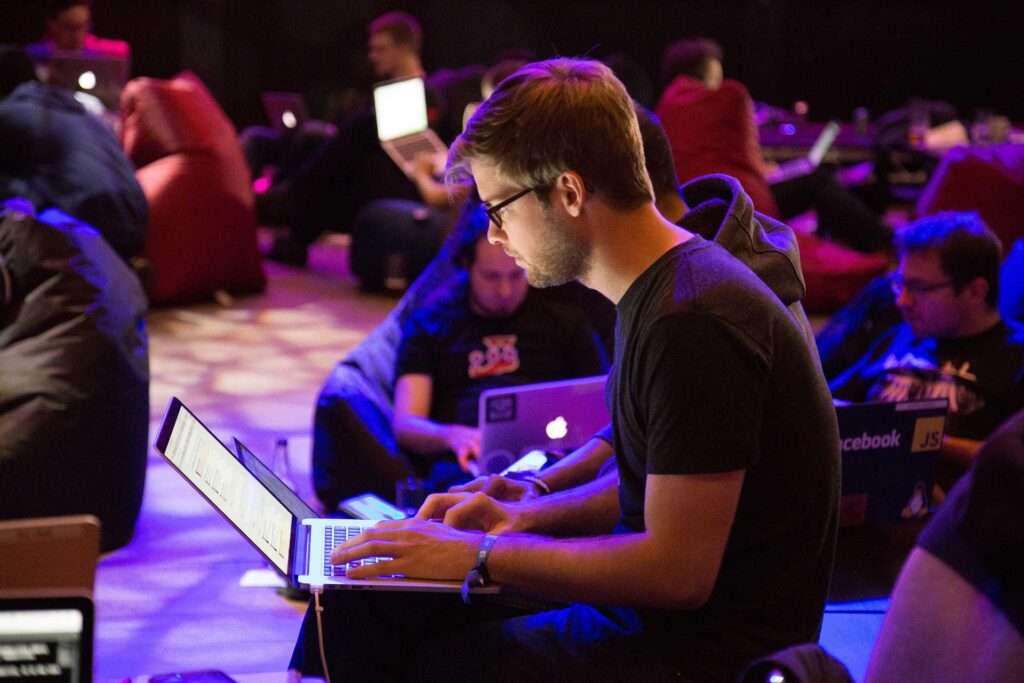
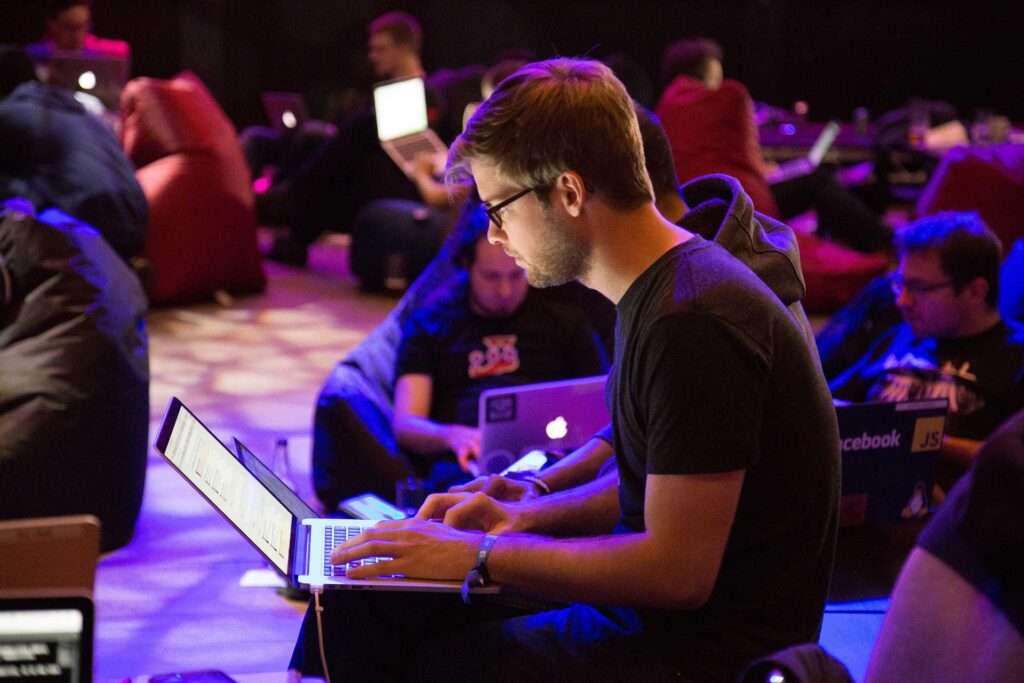
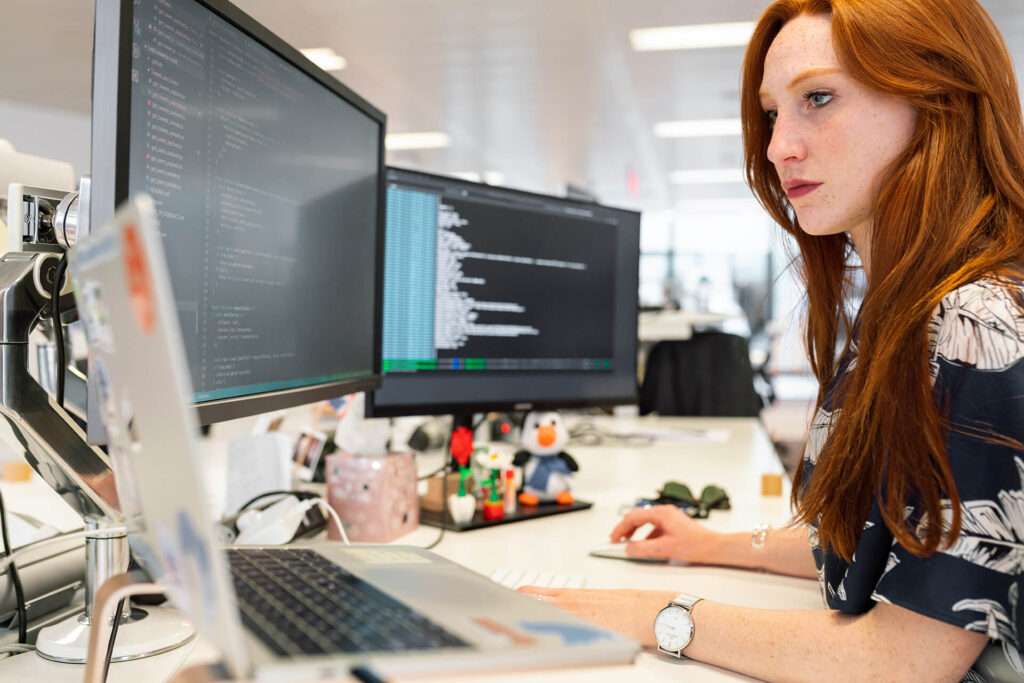
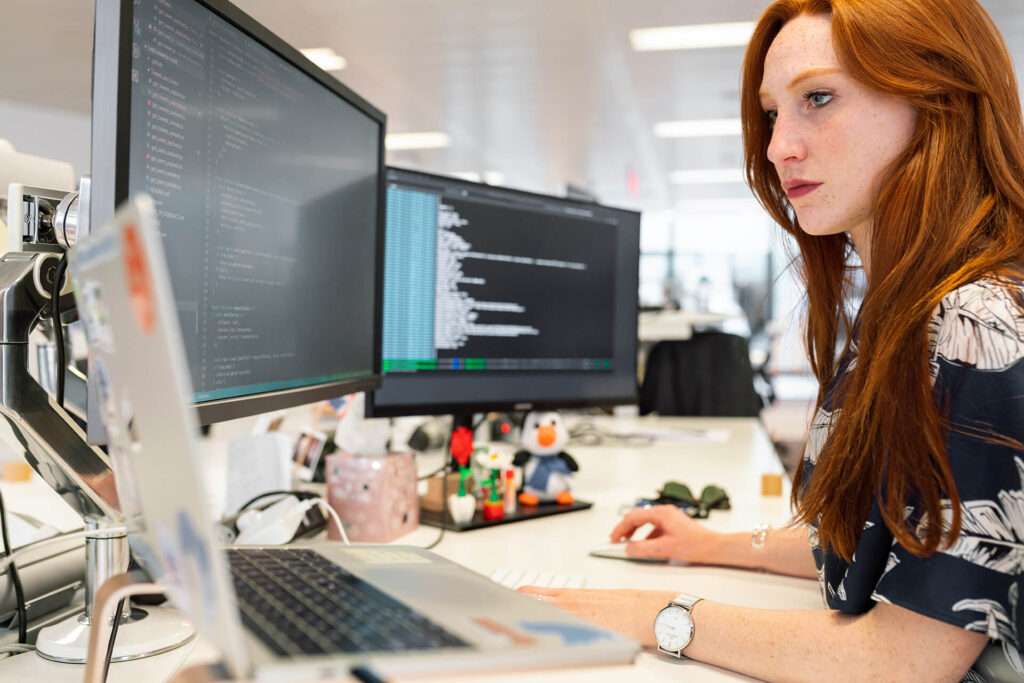
To summarize before deciding to invest in expensive solutions following need to be ensured:
- Evaluate the organization in terms of people skills and expertise. At some level integrity check may also be required
- Evaluate the processes in place, identify loopholes and make necessary changes required to make the processes simple and easy to monitor
- Evaluate existing systems in place in terms of how the same are facilitating monitoring and evaluation as well as the utilization of the same
- Any new system proposed may be validated in terms of its utility and integration with the existing resources, people, processes and system
ammad96
best article thanks joyn
ammad96
waiting for next article